All production processes in view
In a capital-intensive production company like MEISTERWERKE, there are numerous approaches to making one’s own actions more sustainable – while always balancing economic utility with ecological relevance. After all, what is ecologically good is not necessarily successful in economic terms, and vice versa. It is crucial to always take sustainability criteria into account, in addition to the traditional dimensions of time, costs and quality, when designing production processes. MEISTERWERKE wants to consistently lead the way in this area and to further expand the activities initiated in recent years.
Focus on energy management
One of the most important measures in the company is the continuous reduction of energy consumption. To achieve transparency and fully utilise potential, MEISTERWERKE has invested in documenting energy input and output consumption at almost every plant. Electricity consumption is recorded as well as the required heat energy. For Dr Jan Puttfarken, Director Operational Management at MEISTERWERKE, this is a necessary step towards sustainable energy management: “With the installation of the system and the detailed information gained from it, we are gaining maximum transparency and can systematically optimise our energy consumption. But reducing consumption is just one aspect of energy management – it is equally important to increase our energy efficiency by continuously increasing our plant productivity.” MEISTERWERKE is currently working with experts from external specialist companies on a comprehensive energy concept that will enable it to economically and ecologically optimise fulfilment of future electricity and heating requirements for the entire corporate group.
“With the installation of the system and the detailed information gained from it, we are gaining maximum transparency and can systematically optimise our energy consumption. But reducing consumption is just one aspect of energy management – it is equally important to increase our energy efficiency by continuously increasing our plant productivity.”
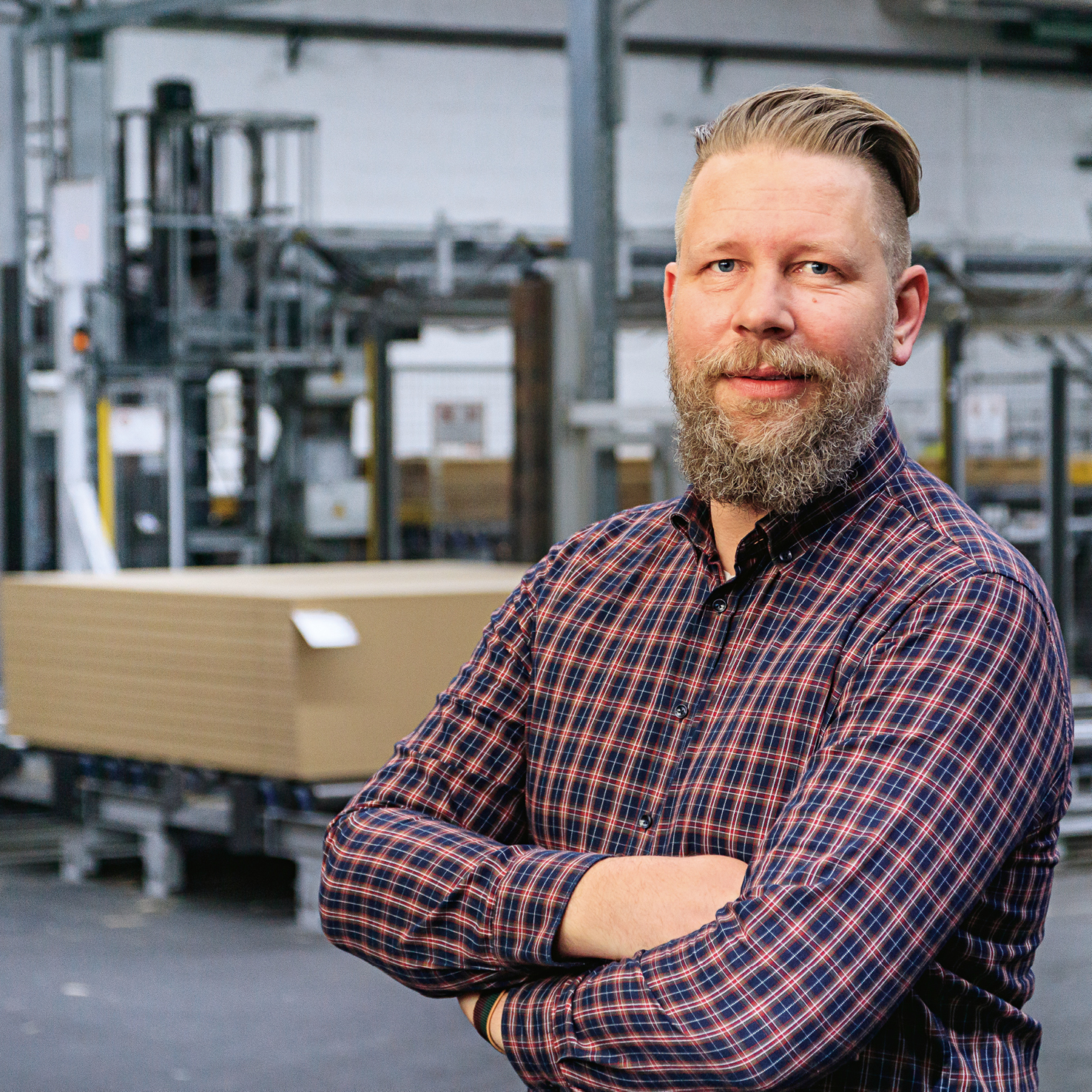
In addition, MEISTERWERKE is gradually converting all indoor and outdoor lighting on the company premises to LED technology, which consumes up to 80 percent less electricity than conventional lights. The focus of this investment from an economic perspective was initially on the production halls, where work is performed in a 3-shift system. In addition, optimised circuitry was installed in individual halls in order to supply areas with power and light only when production is actually being done. Regulation and dimming sensors have been installed in outdoor areas to further reduce electricity consumption.
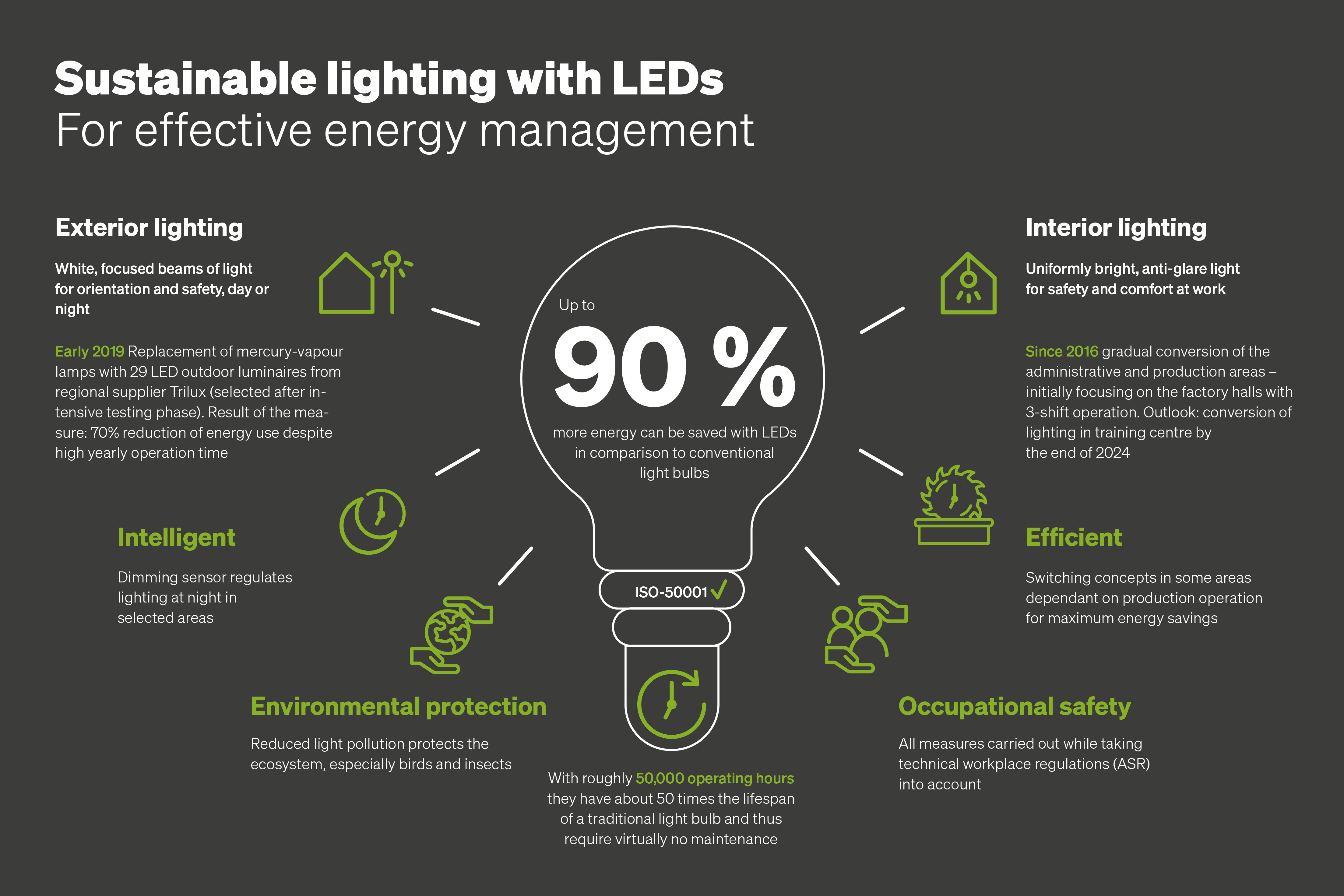
Carbon emissions further reduced
With approx. 50 percent of goods dispatched in-house, MEISTERWERKE is one of the few companies in the industry to rely on its own fleet of trucks. This is an area of the company that has proven its value in terms of service and quality, but which has a considerable impact on the company’s carbon footprint. To continuously reduce carbon emissions in this part of the value chain, MEISTERWERKE relies on professional vehicle fleet management. Each of the 26 company-owned trucks meets Euro 6 emissions standards. Newly acquired vehicles are also equipped with the latest assistance systems which, in addition to the advanced engine technology, ensure lower fuel consumption. The technical advancements are flanked by annual individual driver training courses, which, in addition to teaching driving safety aspects, also deal with the topic of anticipatory driving. Careful handling of wear parts such as brakes and tyres as well as correctly timed gearshifts cut 10 to 15 percent off fuel consumption per 100 kilometres and significantly extend the service life of the vehicles. All told, these measures mean that fuel consumption figures for the MEISTERWERKE truck fleet are well below the average Fleetboard benchmark (fleet management system from Mercedes Benz).
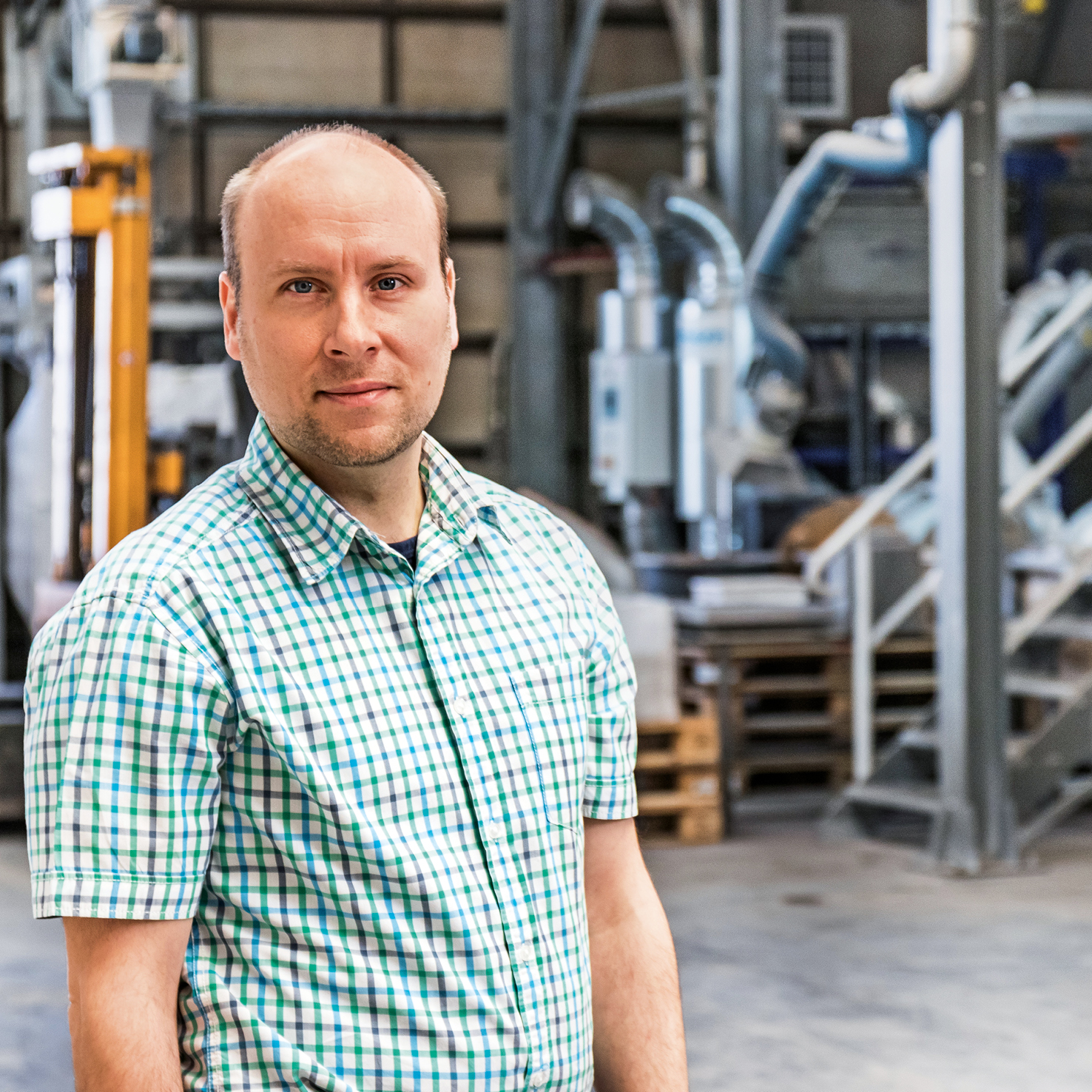
“We tested various electric vehicles a few years ago but concluded that they had various disadvantages compared to conventionally powered forklifts. Only the rapid technological development has enabled us to increasingly use electric vehicles today in internal logistics.”
While there is still no viable alternative for diesel technology in heavy-duty transport today, the approximately 100 industrial forklift trucks used in internal transport are increasingly being converted to electric drive. “We tested various electric vehicles a few years ago but concluded that they had various disadvantages compared to conventionally powered forklifts. Only the rapid technological development has enabled us to increasingly use electric vehicles today in internal logistics,” said Holger Zeiske, Environmental Officer at MEISTERWERKE.
The increased purchase of green electricity also contributes significantly to reducing emissions in the company: Despite the three percent increase in electricity consumption due to capacity utilisation in 2020 compared to the previous year, the resulting carbon emissions were reduced by 31 percent.
Significant reduction in the use of plastics for packaging
In addition to saving energy, a number of initiatives have been launched to reduce the use of plastic in the packaging of finished goods and for secure transport on pallets. By reducing the thickness of shrink-wrapping film, around 98 tonnes of plastic was saved in 2020 alone. From 2022 on, all printed advertising materials, including catalogues and price lists, will be made exclusively from recycled paper, which requires 70 percent less water and 60 percent less energy in the production process than virgin fibre paper used in the past. The Blue Angel also guarantees that no harmful chemicals or optical brighteners are added to the paper during production.